Colmec’s “just in time blending system”, solves compound shelf life issues. Master Batches to which accelerators will be added just before extrusion can be homogenized and fed to the extruder with this device. Being able to stock large volumes of Master Batches of different formulations and being able to use them for only the amount needed is a significant economic advantage.
This system allows the technologist to easily modify and refine the properties of the final compound on the fly. The proportions of master batch and accelerator can be varied in real time improving the efficiency of the extrusion line as a function of extrudate size, temperature, and curing time.
This method produces a high-quality extruded product with reduced energy costs compared with the traditional compounds and extrusion systems. There is a significant economic advantage in making only the (long shelf life) master batch instead of the completed (short shelf life) final compound in the compounding room. In addition the completed compound when made in the mixing room involves accurate temperature control that can reduce production volumes.
This innovative system consists of a patented CTM Mixer, which in about 2 minutes homogenizes the master batch with the accelerant in the proper proportions, transforming it into the final compound.
The final compound from the CTM passes to the CTE conical screw feeder that continuously feeds the extruder.
The Colmec’s “Just in time blending system” offers the extrusion company the ultimate flexibility in final compound properties while maintaining perfect repeatability and traceability.
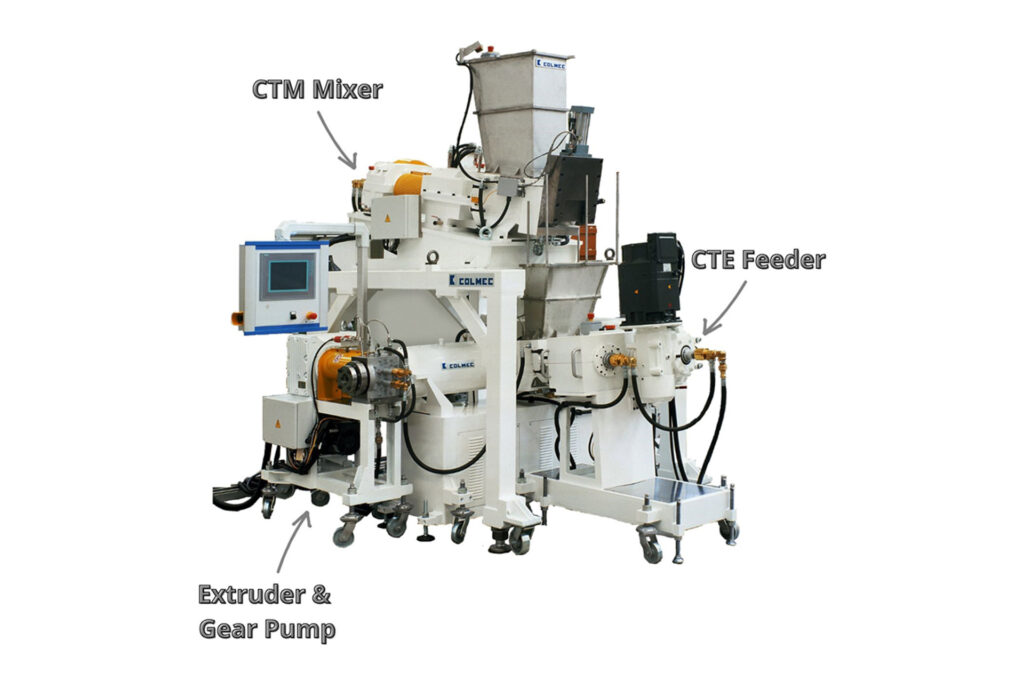